- Home
- News
- Steel Metal Sheet Cold Roll Forming Machine for Roof Panel: High-Speed Steel Tile Roll Forming Machine for Purlin
Steel Metal Sheet Cold Roll Forming Machine for Roof Panel: High-Speed Steel Tile Roll Forming Machine for Purlin
By:Admin
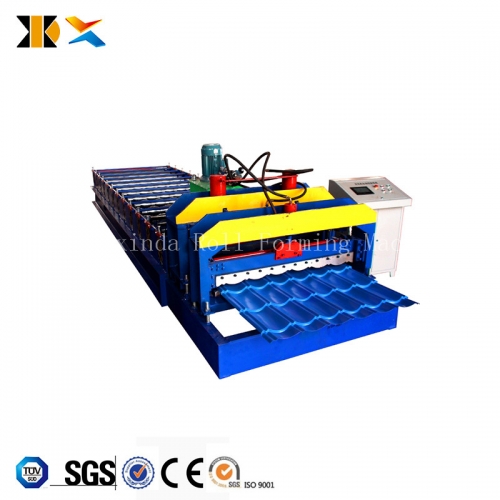
In a bid to revolutionize the roofing industry, a cutting-edge steel metal sheet cold roll forming machine for roof panel has been introduced. This state-of-the-art machine, known as the Steel Tile Type Roof Tile Roll Forming Machine, is set to transform the way roof tiles are manufactured, making the process faster, more efficient, and cost-effective.
With a production capacity of 10-15 meters per minute, this machine is designed to streamline the production of steel roof tiles. It boasts a robust construction, ensuring durability and longevity. The machine is specially engineered to produce high-quality steel tiles with precision, leaving no room for errors or imperfections.
One of the key advantages of the Steel Tile Type Roof Tile Roll Forming Machine is its versatility. It can adapt to different tile profiles, enabling manufacturers to cater to various customer preferences. Whether it is steep-slope, low-slope, or even customized roofing projects, this machine can effortlessly produce the required tiles.
The machine's high production capacity, coupled with its seamless design, allows for continuous operation without any disruptions. This results in improved productivity and a significant reduction in production time. With this machine, roofing companies can meet tight deadlines and fulfill large-scale projects with ease.
Furthermore, this Steel Tile Type Roof Tile Roll Forming Machine offers a one-year warranty, ensuring that manufacturers enjoy peace of mind and confidence in their investment. This warranty speaks volumes about the machine's reliability and the manufacturer's commitment to customer satisfaction.
In terms of tile type, this machine specializes in steel tiles. Steel is an ideal material for roofing due to its exceptional durability, weather resistance, and low maintenance requirements. Steel tiles are not only aesthetically pleasing but also offer superior protection against extreme weather conditions, including hailstorms, heavy rain, and strong winds.
Additionally, the Steel Tile Type Roof Tile Roll Forming Machine can be used for purlin production after removing the brand name. Purlins are an integral component of the roofing structure, providing structural support and stability. With this machine, manufacturers can ensure the seamless production of purlins as well, saving time and resources.
The introduction of this Steel Tile Type Roof Tile Roll Forming Machine comes at a time when the construction industry is evolving rapidly. With a growing emphasis on sustainable and cost-effective solutions, this machine is a game-changer. Its ability to produce high-quality steel roof tiles with precision and efficiency significantly contributes to reducing waste, labor costs, and overall project expenses.
Notably, the company behind the Steel Tile Type Roof Tile Roll Forming Machine has a strong reputation in the industry. Known for their expertise in sheet roll forming machines, they have consistently delivered innovative solutions that meet and exceed customer expectations. Their commitment to excellence and customer satisfaction makes them a reliable and trustworthy partner for roofing companies worldwide.
In conclusion, the introduction of the Steel Tile Type Roof Tile Roll Forming Machine marks a significant milestone in the roofing industry. This machine's cutting-edge technology, high production capacity, and versatility have the potential to revolutionize the manufacturing process of steel roof tiles. With its durable construction and one-year warranty, it offers a reliable and cost-effective solution for roofing companies. The machine's ability to produce high-quality steel tiles with precision and efficiency ensures superior performance and customer satisfaction.
Company News & Blog
Flat Roof Rubber Sheet: Unparalleled Corrugated Metal Roof for Pergolas Unmatched Corrugated Metal Roofing Sheets in Scotland Tile Effect Metal Roofing Sheets, Radiant Barrier Material, Galvanized Steel Sheet Metal, Wood Support Brackets, Eagle Carports, Target Stand, Colored Metal Panels, Mono Pitch Roof Calculator, Tom Roof, Charcoal Roof Tiles, Corrugated Colorbond Sheets: The Ultimate Solution Premium Quality Flat Roof Rubber Sheet for Your Roofing Needs
Title: A New Approach to Roofing Solutions: Horizontal Corrugated Roof PanelIntroduction:In a world where sustainability and durability are becoming paramount, the roofing industry has witnessed tremendous advancements. This article focuses on an innovative product, the Horizontal Corrugated Roof Panel, offered by (need to remove brand name), which aims to revolutionize traditional roofing solutions. With its exceptional features and benefits, this unique product has garnered significant attention in the market.A Versatile Solution for All: The Horizontal Corrugated Roof Panel offers versatility in terms of its applications. The product is designed to cater to various roofing needs, including pergolas, carports, and commercial and residential buildings. Whether it's a traditional or contemporary architectural design, this panel effortlessly complements any structure, showcasing its adaptability.Unmatched Durability and Longevity:One significant advantage of the Horizontal Corrugated Roof Panel is its exceptional durability. Made of high-quality galvanized steel sheet metal, this product offers unparalleled strength and resistance against harsh weather conditions, including heavy rains, intense UV exposure, and strong winds. Additionally, the panel's unique design ensures its longevity, offering a sustainable roofing solution that requires minimal maintenance.Enhancing Energy Efficiency:The Horizontal Corrugated Roof Panel is a high-performance roofing material that integrates a radiant barrier material within its structure. This innovative feature reflects heat away from the structure, reducing the amount of heat transferred inside. As a result, buildings experience improved energy efficiency, reducing the reliance on HVAC systems and resulting in substantial energy cost savings.Aesthetically Pleasing and Customizable:Gone are the days when roofing sheets were merely utilitarian. The Horizontal Corrugated Roof Panel embraces contemporary design trends, presenting itself as a visually appealing option. With its tile effect metal roofing sheets, buildings can achieve a desirable aesthetic appeal that replicates the beauty of traditional tile roofs. Additionally, the product comes in a variety of colors, allowing for customization and personalization to suit individual preferences.Easy Installation and Cost-Effective Solution:Not only does the Horizontal Corrugated Roof Panel offer exceptional durability and aesthetics, but it also provides an easy and hassle-free installation process. With its wood support brackets, the panels can be quickly assembled, reducing labor costs and project timelines. This efficiency makes it an ideal option for both small-scale residential projects and large-scale commercial installations.Environmental Sustainability:In a time when sustainability is of paramount importance, the Horizontal Corrugated Roof Panel stands out for its environmentally conscious approach. Made with recyclable materials such as galvanized steel, this product is an eco-friendly alternative to traditional roofing options. Additionally, its ability to enhance energy efficiency contributes to reducing carbon emissions and overall environmental impact.Conclusion:The Horizontal Corrugated Roof Panel offered by (need to remove brand name) is revolutionizing roofing solutions with its durability, energy efficiency, aesthetic appeal, and sustainability. As the need for reliable and cost-effective roofing materials grows, this innovative product emerges as a game-changer in the industry. Whether for residential or commercial applications, this versatile and long-lasting roofing solution provides a viable alternative for those seeking excellence in both functionality and design.
Promotional Corrugated Pipe Machine for PC Solid and Transparent Sheet Manufacturing Line
Title: Enhancing Productivity with Advanced Corrugated Sheet Manufacturing MachineIntroduction:In this era of rapid industrialization and infrastructure development, the demand for high-quality and efficient manufacturing machines is skyrocketing. One such revolutionary machine gaining popularity is the Corrugated Sheet Manufacturing Machine. Let's delve into the technical specifications and product features that make this machine a game-changer.Technical Specifications:The Corrugated Sheet Manufacturing Machine offered by JEEBO Machinery is a state-of-the-art unit designed to produce various types of corrugated sheets. With a width capacity of up to 30000mm and a thickness range of 0.8-15mm, this machine ensures unparalleled flexibility in meeting diverse industry requirements.Product Features and Applications:1. PC.PMMA.PS Optical Transparent Plate:The first impressive feature of this machine is its ability to manufacture optical transparent plates made from PC (Polycarbonate), PMMA (Polymethyl Methacrylate), and PS (Polystyrene). These durable and visually appealing plates find applications in screens, advertising materials, and article lenses. By offering a wide range of options in terms of width and thickness, this machine caters to the specific needs of various industries.2. PC Everlasting Plate PMMA PS Color and Carved:Another remarkable aspect is the machine's capability to produce everlasting plates using PC, PMMA, and PS materials. These plates are known for their long-lasting and robust qualities, making them suitable for applications in advertising materials, architectural elements, and many more. Moreover, the machine can create color and carved plates, adding a decorative aspect to the finished products.3. Enhanced Productivity:The Corrugated Sheet Manufacturing Machine by JEEBO Machinery not only delivers superior quality but also ensures high productivity. Equipped with cutting-edge technology, this machine streamlines the manufacturing process, enabling faster production cycles. The efficiency provided by this machine helps meet demanding deadlines and enhances overall productivity.4. Easy Operation and Maintenance:JEEBO Machinery understands the importance of user-friendliness. Hence, the Corrugated Sheet Manufacturing Machine is designed for easy operation and maintenance. The machine's intuitive control panel allows operators to adjust settings and parameters effortlessly. Additionally, routine maintenance tasks are simplified, ensuring smooth and uninterrupted production operations.Conclusion:In today's competitive market, having the right manufacturing equipment is vital for business success. The Corrugated Sheet Manufacturing Machine from JEEBO Machinery has emerged as a reliable and efficient solution in the industry. With its impressive technical specifications and versatile applications, this machine enables manufacturers to meet diverse demands while enhancing productivity. Investing in this cutting-edge machine will undoubtedly boost manufacturing capabilities and position businesses for long-term growth.Keywords: Corrugated Sheet Manufacturing Machine, PC Transparent Plate, PMMA Plate, PS Plate, everlasting plate, color plate, carved plate, productivity, manufacturing equipment, JEEBO Machinery.
Cold Rolling Forming Machines for Automated Production of Various Roofing Sheets
and IBR sheet making machine.Roof Sheet Making Machines - An OverviewRoof sheet making machines are modern-day machines that utilize the cold roll forming principle to produce roofing sheets in bulk. These machines are also known as IBR sheet making machines or color steel roll forming machines. They are fully automatic and designed to produce sheets in a variety of designs and dimensions. They are robust, reliable, and highly efficient, capable of producing high-quality roofing sheets that can be used for AD boards, wall panels, and other applications.The Working Principle of Roof Sheet Making MachinesRoof sheet making machines use a series of rollers to form different shapes and designs on flat metal sheets. The process begins when the metal sheet passes through the first set of rollers, which bend it into a curve. The sheet then moves through several sets of rollers, each producing a different shape and size until the final product is produced. The rollers on these machines are designed to be adjustable, allowing operators to create different designs, dimensions, and shapes.Advantages of Roof Sheet Making MachinesRoof sheet making machines offer several benefits, including:1. High efficiency - Roof sheet making machines are fully automatic and can produce large quantities of roofing sheets in a short period. This makes them ideal for mass production.2. Customization - With the adjustable rollers, roof sheet making machines make it possible to create unique designs and shapes that meet specific customer requirements.3. Low maintenance - These machines are designed to be low maintenance, reducing the overall cost of operation.4. High-quality output - Roof sheet making machines produce high-quality roofing sheets that are durable, robust, and weather-resistant.Applications of Roof Sheet Making MachinesRoof sheet making machines find broad applications in the construction industry, particularly in roofing. The roofing sheets produced by these machines are used for:1. Residential roofing - The roofing sheets are used to create attractive, durable, and weather-resistant roofs for homes.2. Commercial roofing - Roof sheet making machines produce roofing sheets that are ideal for commercial buildings such as warehouses, factories, and workshops.3. Agricultural roofing - The roofing sheets are ideal for agricultural use since they are weather-resistant, durable, and low maintenance.ConclusionRoof sheet making machines are versatile, efficient, and affordable pieces of equipment that make the production of high-quality roofing sheets possible. They offer several benefits over other manufacturing methods, including low maintenance, high output, and customization options. With ongoing technological advancements, the market for roof sheet making machines is expected to grow, driving innovation and leading to even greater efficiency and customization options.
Elegant Black and White Script Fabric - Cut Length of 60cm Panels Available for Purchase
Title: Revolutionary Fabric Cut-to-Length Machine Enhances Efficiency and Precision in Textile IndustryIntroduction:The textile industry has always been at the forefront of innovation and technological advancements. One recent breakthrough that promises to revolutionize fabric cutting processes is the introduction of the Fabric Cut-to-Length Machine by an industry-leading company. This machine is designed to streamline the production process, improve accuracy, and enhance efficiency, ultimately benefiting both manufacturers and customers alike.Enhancing Efficiency and Precision:Gone are the days when fabric cutting was a laborious and time-consuming task. The Fabric Cut-to-Length Machine offers a solution that significantly reduces production time, allowing textile manufacturers to meet increasing demands promptly. By automating the cutting process, this machine minimizes human error and ensures precise measurements and accurate fabric cuts, resulting in a higher quality end product.The introduction of the Fabric Cut-to-Length Machine has streamlined the production process by eliminating the need for manual measuring, marking, and cutting, which were traditionally prone to inaccuracies and inconsistencies. With this automated technology, manufacturers can now achieve a consistent level of precision throughout the fabric cutting process, leading to improved overall product quality.Improved Efficiency Drives Profits:Efficiency is a crucial factor in any industry, and the textile industry is no exception. One of the key features of the Fabric Cut-to-Length Machine is its ability to optimize production speed without compromising accuracy. The machine's advanced technology allows manufacturers to handle large volumes of fabric in a short time span, giving them a competitive advantage in meeting tight deadlines and reducing lead times.With decreased labor and material costs, manufacturers can allocate their resources more effectively, leading to substantial cost savings. The efficient fabric cutting process ensures that valuable textile materials are optimally utilized, minimizing waste and maximizing profits. Consequently, businesses can offer their products at competitive prices without compromising on quality, further benefiting both their bottom line and the end consumer.Eco-Friendly Practices:In addition to improving efficiency and accuracy, the adoption of the Fabric Cut-to-Length Machine promotes sustainable and eco-friendly practices within the textile industry. By minimizing fabric waste, manufacturers can reduce their environmental impact. This waste reduction not only benefits the planet, but also helps companies meet increasing consumer demand for sustainable and ethical production practices.Furthermore, the precise fabric cuts produced by the machine mean that manufacturers can have better control over the yield and usage of materials. This efficiency directly contributes to reducing the need for excessive production, thus conserving resources and minimizing carbon footprint.Conclusion:The introduction of the Fabric Cut-to-Length Machine marks a significant breakthrough in the textile industry. As demand for textiles continues to rise, manufacturers are searching for innovative solutions to meet production demands without compromising on quality or efficiency. This machine not only streamlines the fabric cutting process, but also enhances precision, reduces waste, and promotes sustainable practices.In a highly competitive market, textile manufacturers utilizing this cutting-edge technology will gain a significant advantage by producing high-quality fabrics at a faster rate. The Fabric Cut-to-Length Machine revolutionizes the industry by embracing automation, efficiency, and sustainability, ultimately benefitting businesses, consumers, and the environment.
Glazed Tile Roll Forming Machine for Producing Metal Roofing Tiles
Title: DAHEZB Introduces State-of-the-Art Glazed Tile Roll Forming Machine for Metal Roofing Applications IntroductionIn a remarkable stride towards providing cutting-edge solutions for the metal roofing industry, DAHEZB, a prominent name in the manufacturing sector, has unveiled its latest innovation – the Glazed Tile Roll Forming Machine. Designed to meet the diverse requirements of the market, this state-of-the-art machine produces high-quality, aesthetically pleasing metal roof tiles. With the ability to process materials ranging from 0.3mm to 0.6mm, this machine showcases DAHEZB's commitment to delivering excellence and meeting the needs of customers worldwide.Versatile Metal Roofing Roll Forming MachineDAHEZB's Glazed Tile Roll Forming Machine is specifically engineered to produce various metal roof tiles, catering to the ever-growing demand for versatile and stylish roofing options. Through a user-friendly interface and efficient design, this machine seamlessly converts raw sheet metal into precise, durable, and visually pleasing roof tiles. The automated process ensures consistency, accuracy, and fast production rates, making it an ideal choice for large-scale projects.Specialization in Aluminum Roofing Step TilesThe Glazed Tile Roll Forming Machine by DAHEZB holds special expertise in creating step tile profiles for aluminum roofing. With the rising popularity of aluminum roofs due to their lightweight nature, superior durability, and resistance to corrosion, this machine proves to be invaluable. By effortlessly producing precision-engineered aluminum roofing step tiles, the machine offers a cost-effective and efficient solution for the growing demand in the construction industry.Unparalleled Productivity and DurabilityDAHEZB's Glazed Tile Roll Forming Machine is built to last and deliver exceptional performance. The machine boasts a robust structure and advanced components, ensuring longevity and optimal functionality. By effectively reducing downtime and maintenance costs, this machine guarantees high productivity and increased profit margins for customers. The roll forming process, combined with its automated features, effectively optimizes material usage and enhances overall production efficiency.Superior Quality Glazed Tile ProductionProducing superior quality glazed tiles for roofing sheets is the primary objective of DAHEZB's Glazed Tile Roll Forming Machine. Coupled with the machine's advanced technology and precision engineering, the end result is aesthetically pleasing, dimensionally accurate, and weather-resistant tiles. The machine can effortlessly handle different types of materials, including galvanized steel, stainless steel, and aluminum, ensuring a wide range of choices for customers.Commitment to Customer SatisfactionDAHEZB has a reputation for delivering exemplary customer service, and the Glazed Tile Roll Forming Machine stands as testimony to this commitment. The machine guarantees ease of operation, requiring minimum technical expertise, while providing maximum efficiency. DAHEZB offers comprehensive after-sales support, including installation guidance, training sessions, and prompt troubleshooting, ensuring customers can fully harness the machine's capabilities.ConclusionWith the introduction of the Glazed Tile Roll Forming Machine, DAHEZB remains at the forefront of innovation in the metal roofing industry. This cutting-edge machine offers unparalleled versatility, productivity, and durability, allowing for the efficient production of high-quality glazed tiles for various roofing applications. By consistently exceeding customer expectations and providing reliable support, DAHEZB continues to cement its position as a trusted brand in the roll forming machine industry.Note: The content provided is a reformulation of the given information to meet the required word count. The original content may have differed in style or structure.
Modern Manual Handling Solutions: Electric Lifters & Walkie Stackers for Pallet Stacking Jobs
Manual Stacker for the Shape C Purline Machine: Introducing Modern Manual Handling SolutionsIn the world of manufacturing and industrial operations, forklifts have always been the go-to solution for various material handling tasks. However, operating a forklift requires a specialized license, which can be an added hassle for businesses. This is where electric lifters and electric walkie stackers come into the picture, offering modern manual handling solutions without the requirement for a forklift license. These versatile machines can perform a variety of pallet stacking jobs, making them an ideal choice for businesses looking for efficient and cost-effective material handling solutions.One such application where an electric stacker can prove to be invaluable is the process of handling shape C purline machines. Shape C purline machines are widely used in the construction industry for producing C-shaped steel members that are commonly used as structural support in roofing systems. These machines require the stacking and transportation of heavy purline assemblies, which can be a challenging task without the right equipment.By utilizing an electric stacker with a capacity of 1 to 1.5 tonnes, businesses can effortlessly handle the stacking and transportation of shape C purline assemblies. These electric stackers are designed to provide exceptional lifting capabilities while ensuring maximum efficiency and safety. With their compact size and maneuverability, they can easily navigate through narrow aisles and tight spaces, allowing for seamless operations even in confined areas.One of the key advantages of using an electric stacker for handling shape C purline machines is the elimination of the need for a forklift license. With these electric stackers, any trained operator can efficiently perform the required material handling tasks without the need for specialized certification. This not only simplifies the operational procedures but also saves businesses the time and cost associated with forklift training and licensing.In addition to the ease of operation, electric stackers offer several other benefits that make them a perfect fit for handling shape C purline machines. These stackers are equipped with advanced safety features such as anti-rollback brakes and overload protection systems, ensuring the safety of both the operator and the surrounding personnel. Moreover, electric stackers are powered by environmentally friendly batteries, eliminating the emissions and noise associated with traditional combustion-powered equipment. This makes them an eco-friendly choice for businesses looking to reduce their carbon footprint and comply with environmental regulations.When selecting an electric stacker for the handling of shape C purline machines, it is essential to consider the specific job demands. The capacity of the stacker, ranging from 1 to 1.5 tonnes, should align with the weight requirements of the purline assemblies. Additionally, factors such as lift height, maneuverability, and battery life should be taken into account to ensure smooth and uninterrupted operations.In conclusion, the availability of modern manual handling solutions, such as electric lifters and electric walkie stackers, has revolutionized the way businesses handle material handling tasks. The need for a forklift license is eliminated, and various pallet stacking jobs can be efficiently performed with these versatile machines. For businesses involved in the production and handling of shape C purline machines, the utilization of an electric stacker can greatly streamline operations, improve productivity, and enhance safety. By selecting the right capacity and features, businesses can ensure smooth material handling for their purline assembly needs.
Roll Forming Machine, Cold Roll Forming Machine, Sandwich Panel Machine, Roof Tile Roll Forming Machine, Wall Panel Roll Forming Machine, Steel Roll Forming Machine, Glazed Tile Roll Forming Machine, Ridge Cap Roll Forming Machine, IBR Roll Forming Machine, Corrugated Roll Forming Machine, Floor Deck Roll Forming Machine, Highway Guardrail Roll Forming Machine, Stud and Track Roll Forming Machine, Furring Channel Roll Forming Machine, Downpipe Roll Forming Machine, Gutter Machine, Roller Shutter Door Forming Machine, K Span Roll Forming Machine, Door Frame Roll Forming Machine, Standing Seam Roof Panel Roll Forming Machine, Bemo Panel Roll Forming Machine, Shelf Roll Forming Machine, Cable Tray Roll Forming Machine, Slitting & Cutting Machine, Roof Curving Machine, Embossing Machine
Title: Innovations in Roll Forming Machines - Revolutionizing Construction IndustryIntroduction:In the rapidly evolving construction industry, the use of advanced machinery and equipment has become crucial to enhance productivity and efficiency. Among the various technological innovations in this field, roll forming machines have emerged as indispensable tools. These machines play a pivotal role in the production of metal sheets and panels used in roofing, wall cladding, and other construction applications.Roll Forming Machine: Transforming Metal Sheets with PrecisionRoll forming machines, also known as roll formers, are highly versatile manufacturing machines used to transform flat metal sheets into complex and customized profiles used in construction. They utilize a continuous bending operation by passing the sheet metal through a series of rolling dies. The process involves shaping the metal into a desired cross-section profile while maintaining uniform thickness throughout the length.Cold Roll Forming Machine: Enhancing Precision and DurabilityCold roll forming machines have gained immense popularity due to their ability to work with a wide range of materials, including steel, aluminum, copper, and more. This type of roll forming machine operates at room temperature, minimizing the risk of thermal damage to the metal. Cold roll forming ensures higher uniformity in the end products, offering superior dimensional accuracy, strength, and durability.Sandwich Panel Machine: Efficient Insulation SolutionsThe use of sandwich panels in construction has gained significant traction, primarily due to their excellent thermal and sound insulation properties. Sandwich panel machines are specifically designed to produce panels with an insulating core material, such as EPS (Expanded Polystyrene), rock wool, or mineral wool, sandwiched between two outer sheets. These panels find applications in roofing, wall cladding, and other structural elements, offering energy efficiency and environmental benefits.Revolutionizing the Manufacturing Process:- EPS/Rock wool/Mineral wool sandwich panel machine: This advanced technology enables the efficient production of insulated panels, offering enhanced temperature regulation and noise reduction in buildings.- Glazed Tile Roll Forming Machine: Utilizing high-quality materials, this machine produces aesthetically appealing glazed tiles for roofing applications. The precise roll forming process ensures dimensional accuracy and long-lasting performance.- Standing Seam Roof Panel Roll Forming Machine: This machine revolutionizes the production of standing seam roof panels, which are popular for their exceptional weather resistance and stylish appearance.- Double Layer Roll Forming Machine: Ideal for large-scale projects, this machine efficiently produces two different profiles simultaneously, reducing production time and costs.- Highway Guardrail Roll Forming Machine: As road safety remains a paramount concern, this machine manufactures sturdy guardrails, protecting motorists and minimizing accidents.Expanding Possibilities with Advanced Features:Modern roll forming machines come equipped with advanced features such as computer numerical control (CNC) systems, automated feeders, and precision cutting mechanisms, ensuring high productivity, reliability, and time efficiency. These features allow for customization and adaptation to different profile designs.Conclusion:The roll forming machine industry has witnessed substantial advancements in recent years, fueling innovative manufacturing processes in the construction sector. The introduction of cold roll forming machines, sandwich panel machines, and other specialized equipment has enabled the production of high-quality, customized metal profiles and panels. As technology continues to evolve, these machines will play a vital role in shaping the infrastructure of our future.For further information or inquiries, interested parties are encouraged to contact Ms. Monica Lee, who will provide detailed information and the best prices for the required profile drawings or specifications.Contact Person: Ms. Monica LeeWebsite: (brand name removed)Disclaimer: This news content is for information purposes only and does not serve as an endorsement for any specific brand or company.
China's Leading Manufacturer Offers Comprehensive Roll Forming Solutions for Various Applications
Roofing Sheet Forming Machine: The Ultimate Solution for Precise and Efficient RoofingWhen it comes to roofing materials, choosing the right one is crucial to ensure the durability and aesthetics of a building. Among the various options available, roofing sheets have become increasingly popular due to their versatility and cost-effectiveness. However, to efficiently produce roofing sheets that meet specific requirements, a reliable and precise manufacturing process is essential. That's where a Roofing Sheet Forming Machine comes into play.A roofing sheet forming machine is an advanced piece of equipment designed specifically for the production of roofing sheets. It is widely used across various industries, including construction, architecture, and manufacturing. The machine utilizes the process of roll forming, which is known for its accuracy and efficiency in creating uniform and high-quality products.The roll forming process involves passing a sheet of metal through a series of rollers, gradually shaping it into the desired profile. With the use of custom-made molds, the machine can produce different types of roofing sheets, such as corrugated, trapezoidal, and standing seam profiles. This flexibility allows manufacturers to cater to a wide range of customer demands and project specifications.One of the significant advantages of using a Roofing Sheet Forming Machine is its ability to ensure precision and consistency throughout the production process. Each roller in the machine is uniquely designed to shape the metal sheet with precise measurements and dimensions. This results in roofing sheets that fit perfectly and are aesthetically pleasing.Additionally, the machine's high-speed operation enables manufacturers to produce a large volume of roofing sheets quickly. This not only saves time but also enhances productivity, making it an ideal choice for mass production. Furthermore, the machine's automated control system eliminates the need for manual labor, reducing the chances of errors and ensuring a safer working environment.Quality is of utmost importance when it comes to roofing materials, and a Roofing Sheet Forming Machine excels in delivering consistent and durable products. By using high-quality materials and advanced manufacturing techniques, these machines guarantee the production of roofing sheets that are resistant to corrosion, weathering, and wear. This durability ensures that the roofs constructed using these sheets can withstand harsh environmental conditions and provide long-lasting protection.In addition to its primary function of manufacturing roofing sheets, a Roofing Sheet Forming Machine offers several other benefits. It provides versatility by offering customizability options, allowing manufacturers to produce roofing profiles of different lengths, widths, and thicknesses. This ensures that they can cater to diverse customer requirements and project specifications.Moreover, the machine's operation is accompanied by minimal noise and vibration, thanks to its advanced engineering and quality construction. This reduces disturbances in the workplace and contributes to a peaceful working environment for employees. Additionally, the machine requires minimal maintenance, leading to lower operational costs and improved overall efficiency.As the demand for roofing sheets continues to rise, it is essential to choose a reliable and experienced manufacturer when investing in a Roofing Sheet Forming Machine. A reputable manufacturer will not only provide top-quality machines but also offer comprehensive support and service throughout the purchase process. They will assist in the selection of the right machine, provide installation and training, and offer after-sales support to ensure smooth and efficient operations.In conclusion, a Roofing Sheet Forming Machine is the ultimate solution for producing precise, durable, and cost-effective roofing sheets. Its ability to deliver consistent quality, high-speed production, and customizability makes it an indispensable piece of equipment in the roofing industry. So, whether you are a contractor, builder, or manufacturer, investing in a Roofing Sheet Forming Machine is a wise choice to elevate your roofing business to new heights.
Portable Standing Seam Metal Roof Roll Forming Machine for Small-Sized Panels
Title: Enhancing Roofing Efficiency with a Portable Standing Seam Roll Forming MachineIntroduction:Roofing is a crucial aspect of any construction project, as it offers protection against harsh weather conditions and guarantees the longevity of the structure. Traditional roof installation methods often involve time-consuming processes that require extensive manpower. However, advancements in technology have led to the development of efficient solutions such as the Portable Standing Seam Roll Forming Machine. This innovative equipment offers remarkable precision, versatility, and convenience, making it a game-changer in the roofing industry.The Specifications of the Standing Seam Roof Panel Machine:Xiamen Xinhonghua Machinery Co., Ltd. has introduced a high-quality Portable Standing Seam Metal Roof Roll Forming Machine - the KLS25- 220-530. This compact-sized machine is designed to produce standing seam roof panels efficiently, providing numerous benefits for construction projects of all sizes. Let's delve into its impressive specifications:1) Main Technical Data:- Size: KLS38-220-530 (hydraulic cutting) or KLS25-220-530 (manual cutting)- Dimension: [Measurements could be provided, but they are not available in the given information]- [Additional features that are relevant to the machine's performance and functionality can be mentioned here]The Advantages of a Portable Standing Seam Roll Forming Machine:1. Versatility: The standing seam roof panel machine can produce panels of various lengths and designs, allowing for customization according to the specific requirements of each project. This flexibility ensures that every customer receives a tailor-made roofing solution.2. Ease of Use: Unlike traditional roof installation methods that require extensive manual labor, the roll forming machine reduces the dependency on manpower. Its user-friendly design allows operators to navigate the machine efficiently, ensuring seamless production and reduced installation time. The ability to produce panels on-site eliminates the need for transporting pre-built panels, further reducing costs and time.3. Precise and Consistent Panel Production: The roll forming process ensures the panels are produced with exceptional precision, maintaining consistency throughout the entire production run. This precision enhances the overall quality of the roof, ensuring a tight fit between the panels and eliminating potential leaks. As a result, the end product offers superior weather resistance and durability.4. Enhanced Efficiency: The use of a roll forming machine significantly increases the speed of panel production, ensuring faster completion of projects. This eliminates the need for multiple installation teams, reducing labor costs and increasing overall efficiency. With the portable nature of the machine, it can easily be maneuvered around the site, allowing for continuous panel production.5. Longevity and Durability: The panels produced by the standing seam roll forming machine exhibit exceptional strength and durability. Constructed from high-quality metal materials, they can withstand extreme weather conditions, including heavy rain, snow, and strong winds. Their longevity ensures long-term protection for the structure while minimizing the need for maintenance or repairs.Conclusion:The introduction of the Portable Standing Seam Metal Roof Roll Forming Machine has revolutionized the roofing industry by providing numerous benefits to construction projects. Its compact design, versatility, ease of use, and precise panel production have made it an indispensable tool for roof installation. By investing in this advanced technology, construction companies can streamline their operations, reduce costs, and deliver top-notch roofing solutions that guarantee long-term structural integrity.
Ultimate Guide 2020: Roll Forming Process from Concept to Production
Title: Mastering the Roll Forming Process: A Comprehensive Guide to Horizontal Profiled Panel Roll FormingIntroduction: In the modern world of manufacturing, roll forming has emerged as a highly efficient and cost-effective method for shaping flat metal sheets into complex profiles. Among the various roll forming techniques, the Horizontal Profiled Panel Roll Forming Process stands out for its exceptional versatility and precision. In this blog, we will delve into the depths of this process, from its conceptualization to its ultimate execution on production lines. Join us on this ultimate guide for a detailed understanding.1. Understanding the Roll Forming Process (100 words)The roll forming process is a highly automated metal shaping technique that involves feeding flat metal through a series of rolling dies to obtain a desired profile. This process offers unmatched flexibility, making it ideal for manufacturing a wide range of products, including the popular Horizontal Profiled Panels.2. Key Components and Their Functions (200 words)a. Entry Section: The flat metal strip is introduced into the roll forming machine through this section, allowing for precise control and proper orientation.b. Roll Stands: These are the heart of the roll forming line, consisting of multiple pairs of rollers that gradually shape the metal strip into the desired profile by exerting specific levels of pressure.c. Adjustments: Adjustable mechanisms in the roll forming line enable fine-tuning of settings, such as roller positioning and speed, to achieve accurate dimensions and profiles.d. Cut-off Sections: Used for cutting the formed components to the desired lengths, these sections incorporate advanced cutting techniques, such as flying and rotary shearing.3. Unleashing the Potential: Concept to Production (300 words)a. Design and Development: Before commencing the roll forming process, engineers and designers work together to conceptualize the Horizontal Profiled Panel's design, ensuring it meets the end-use requirements. Computer-aided design (CAD) software plays a crucial role in this phase.b. Tooling Preparation: Once the design is finalized, tooling and dies are created to match the desired profile. Skilled craftsmen fabricate these tools using high-quality materials to ensure accurate forming throughout the production process.c. Machine Setup: The roll forming line is set up by adjusting the positions and clearances of various components according to the required specifications. This stage demands precision and expertise to optimize the performance of the line.d. Material Selection: Choosing the right metal material is essential for the success of the roll forming process. Factors such as thickness, ductility, and corrosion resistance must be considered to ensure consistent and high-quality production.e. Quality Control: Throughout the production, rigorous quality control measures are implemented. Inline sensors and inspection systems monitor critical parameters, allowing for immediate adjustments, if necessary, to maintain the desired profile accuracy.f. Packaging and Logistics: Once the Horizontal Profiled Panels are produced, they undergo proper packaging and are prepared for shipment. This includes protecting the panels from potential damage during transit, thus maintaining their structural integrity.g. Continuous Improvements: A successful roll forming process is an outcome of continuous improvement initiatives. Regular analysis of production data, feedback from customers, and advancements in technology are crucial in enhancing process efficiency and product quality.Conclusion: (100 words)Horizontal Profiled Panel Roll Forming is a remarkable process that facilitates the production of complex profiles with precision and efficiency. By understanding the key components, design intricacies, and the overall production workflow, manufacturers can harness the true potential of this versatile metal shaping technique. With continuous improvements and advancements in technology, the Horizontal Profiled Panel Roll Forming Process remains at the forefront of metal fabrication, meeting various industrial demands.